gates, fencing, balustrade, security doors, we've got you covered.
Eastern Suburbs Wrought Iron pride ourselves on being honest with our clients - here is a rundown of our process, from the quote stage right through to installation to ensure our clients are given the highest quality service and wrought iron products, be itQuote & Measure
Whether its gates, fencing, balustrade, security doors or other - we generally request information via email & will provide a no-obligation indicative quote for you. We'll conduct a site visit to confirm details, measurements, angles, and pricing upon quote acceptance. Whilst on site we'll carry out a thorough site inspection & measure; and will be available to discuss the job in further detail if required and can answer any questions or queries you may have.
Go ahead
This is where a number of things could happen, we might need to have another meeting to get a few final details sorted & we'll give you our lead time if we haven't already. Generally, we say 4 to 6 weeks. Quality takes time ~ our products are custom made to your job specifications and not something we pick off a shelf and alter to fit. We pride ourselves on meeting our lead times, so if we say it will be 4 to 6 weeks it WILL be in that time (unless unforeseeable circumstances beyond our control occur) we do deliver on our promise.
This process can take up to half the lead time depending on the design etc.
Galvanizing
Now, this is the most important process in our wrought iron products as this is the rust protection. Many companies today are trying to compete against one another, and by cutting costs they cut corners in the process. We don't bother competing with those companies because their products are far inferior to ours. For instance, others use inferior galvanized material which is paper-thin and is only a thin coating which when they cut or drill holes, the end or edge of the galvanized material is left bare metal (refer to the illustration) don't be fooled into this sort of thing. Or they will electroplate, which is an electrical charge that draws the electroplating to the steel but does not get into corners or inside the job which is a pretty poor way to coat when you're paying to have your product last the life of the house. Because it won't.
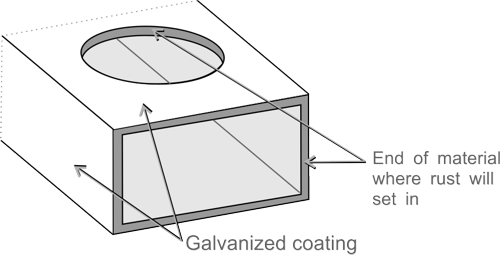
Eastern Suburbs Wrought Iron use top quality steel, all external products are hot-dip galvanized which means that once your product is manufactured it is then sent away to be dipped in a pool of molten zinc which gets inside and outside your job and also covers all holes and edges etc.
So we're not kidding around when we say that our products and workmanship will stand the test of time - because it's the truth about the products we send out of our workshop.
We work to the standard that if it's not good enough to be installed at our own home, it's not good enough to leave the workshop.
Clean up
Once we pick up the job from the galvanizers, we bring it back to the workshop to grind it down, making it free of any sharp or jagged edges.
Coating
The types of coatings available are - powder coating or painting, there is a full range of COLOURBOND® steel colours or Dulux® colours available to ensure your colour of choice is possible.
Installation
We will call you as soon as your job is ready, to organise a suitable day to install.
This is just a quick rundown of our process & how we operate at Eastern Suburbs Wrought Iron - we hope this helps give you an insight into how our quality items are produced.